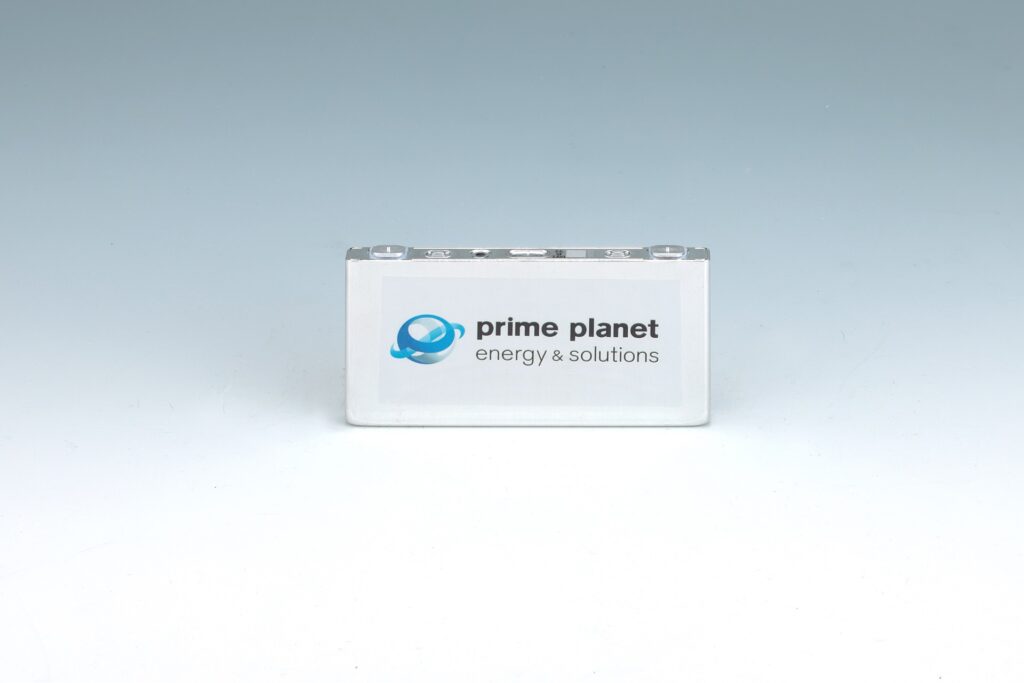
- #PPESの強み
- #インタビュー
- #ハイブリッド
- #ワンチーム
カーボンニュートラルに向けて電動化が進む自動車業界において、急成長が続いていたバッテリーEV(BEV)市場でしたが、2023年度は販売ペースが緩やかに。その一方で、2024年現在、足元ではハイブリッド車(HEV)へ再び注目が集まっています。
こうした状況で、BEV用、HEV用、PHEV用(プラグインハイブリッド車)までバッテリーの幅広いラインナップを展開し、とりわけHEV用バッテリーでは20年以上の出荷実績(※1)と世界トップシェア(※2)を達成しているPPESに、いま大きな期待が寄せられています。PPESの製造拠点では、ものづくりの伝統を活かし、高い生産性と技術力で、安全で高品質・低コストを実現するHEV用バッテリーが量産されています。
1 合弁設立前のパナソニック(三洋電機)での車載用角形電池事業を含む。
2 HEV用リチウムイオンバッテリー、23年生産実績ベース。各種レポートをもとに当社調べ。
「足元では、HEV用バッテリーの引き合いは増えています。バッテリー市場は複雑で、価格や性能だけでなく、お客様(自動車ユーザー)の使用環境、環境意識や国・地域の事情によっても動きます。こうした中で、BEVからHEVまで、柔軟に瞬発力を持ってバッテリーをご提供することで、幅広い地域での脱炭素化に貢献できると考えています」
65Dのプロジェクトマネジメントを担当するY. O.はそう語ります。「121265D」モデル(通称「65D」)は2021年から生産を開始したHEV用バッテリーで、従来製品から大幅な小型軽量化と低コスト化を実現しました。65Dは現在のPPESの主力モデルとして世界中のHEVに広く搭載されています。
世界で戦える標準バッテリーを目指して
65Dの開発当時、PPESは前身のパナソニック、三洋電機時代に築き上げたHEV用バッテリーの高い競争力を、もう一段飛躍させるための挑戦を行っていました。やがて来るBEVの本格普及に備えて、市場拡大が進んでいるHEV用バッテリーで技術を磨き、実績を積み上げ、堅実に事業を伸ばすことが、経営戦略においても、世界の脱炭素社会への移行にとっても重要だと考えたからです。
まず、開発段階で鍵となったのは、バッテリーの標準化です。
65Dが開発されるより前のPPESでは、カーメーカーの細かな要望に合わせて車種ごとにオーダーメイドでバッテリーを開発することが多く、標準化よりも優先される考え方でした。しかし、バッテリーの基本設計において高い性能と品質を担保し、汎用的な構造設計を実現できれば、各車種でフレキシブルに使える「標準バッテリー」となり、大幅なコストダウンと生産までの期間短縮が期待できます。
どうすれば車種横断で使えるバッテリーを実現できるか?
65Dの開発では、2020年のPPESの発足時、パナソニック出身者とトヨタ自動車出身者の合同チームによる「サムライプロジェクト」と呼ばれる取り組みが始動していました。電池メーカーとカーメーカーという壁を壊し、「世界標準を作る」という共通の目標を持って最高のHEVバッテリーづくりを開始しました。
「様々なバックグラウンドを持つ人の集まりでしたが、同じ目標を掲げ、互いのいいところを知り、謙虚に受け入れていく姿勢がお互いにあったからこそ、実現したものだと思います」(Y.O.)
「サムライプロジェクト」では、標準化のほかにも競争力を高める取り組みが随所で行われました。企画から開発・生産準備までのプロセスでは、設計、生産技術、製造、品質管理などの機能別の分業をやめ、一体推進する体制をとりました。こうすることで、部署ごとに試行錯誤するプロセスが減り、大幅なリードタイム短縮を実現。当初4年かかると見込まれていた65Dのプロジェクトは半分の2年で、目標のコスト・品質で量産開始することができました。
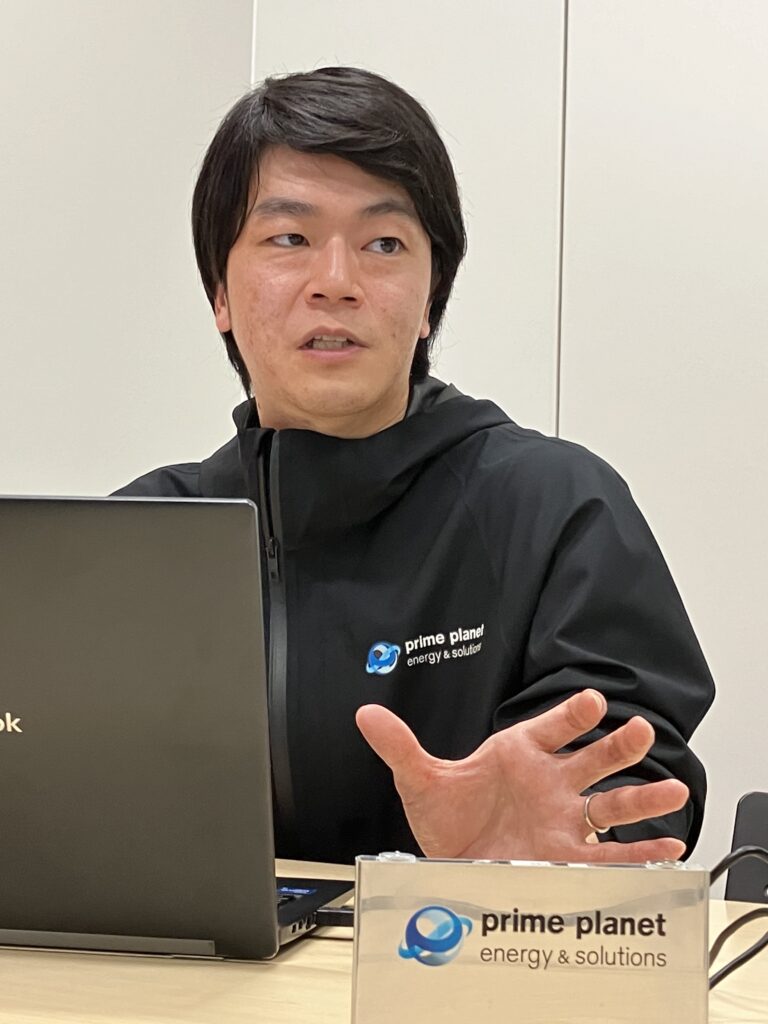
パナソニック・三洋電機から受け継ぐ「強い現場」
量産段階では、設計通りの品質を確保しながら高い生産性を実現できるのかが課題となります。開発段階で予想できなかった問題に柔軟かつ迅速に対処し、競争力を高める核となっているのが、PPESのルーツ、パナソニック・三洋電機時代から続く「強い現場」です。
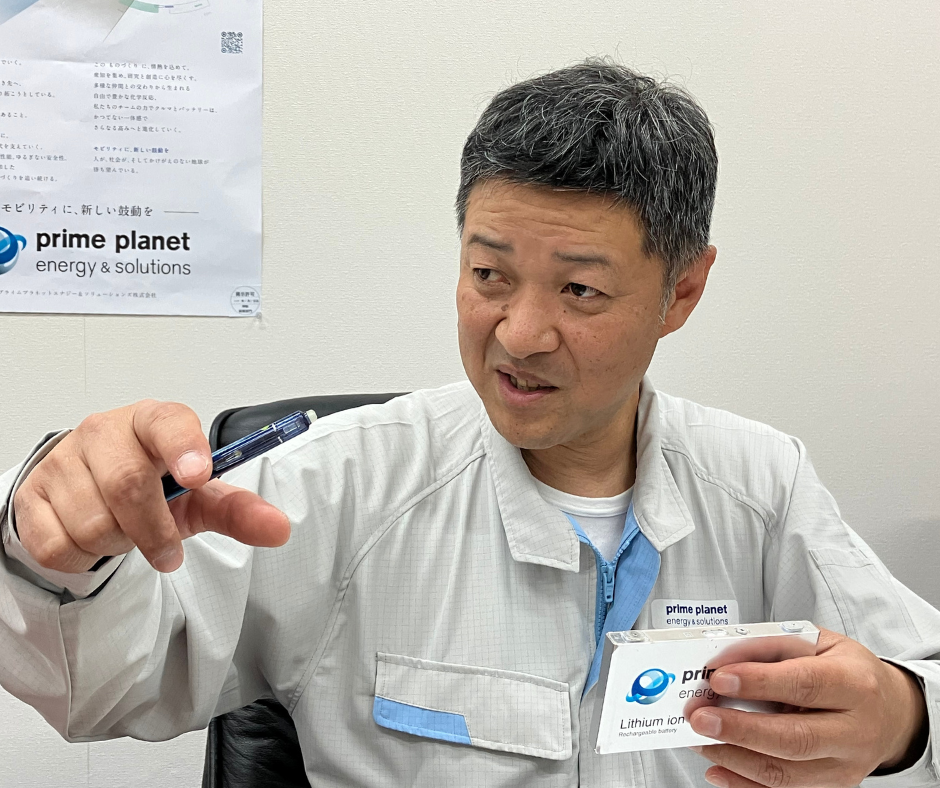
PPESの徳島、洲本拠点の製造現場を統括するK. T.は、製造チームが工程全体に対して当事者意識を持って改善を行うことで、製造の質とスピードが上がり、製品の競争力に繋がると言います。
「製造チームが『自分たちの工程は、自分たちで作り上げていく』という強い意識を持つのは、三洋時代から続く工場の風土みたいなものですね」(K. T.)
工場組織は同じ工程でも製造や保全といった機能ごとに組織があります。しかし、PPESでは、そうした機能を軸とした組織構造にこだわりすぎず、横のつながりを持ったチームで問題の改善や不具合の対処を行うので、迅速な対応が可能となります。
「ラインの立ち上げ直後のころ、電池ケースに電解液を入れるわずか4ミリの穴に、溶接時に出る数ミクロンの金属異物が入り込む不具合がありました。20年培った知見で確実な設備構造としたにも関わらず、想定外の異物の挙動が起こったのです。
対策設備が導入されるまでに半年の期間を要するという事で、それまでの間、生産を継続するためにどうやったら金属異物が混入しない工程ができるか、多くのメンバーで改善策を検討しました。結果、工程内で一時的に注液口をふさぐシール状の蓋を貼り付けることで解決したのですが、そのシールの形状や材質、貼り方ひとつとっても皆の知恵を出し合っています。このように、誰が拾うかわからない三遊間のゴロも、みんなが積極的に飛びついてくれる文化がありますね」(K. T.)
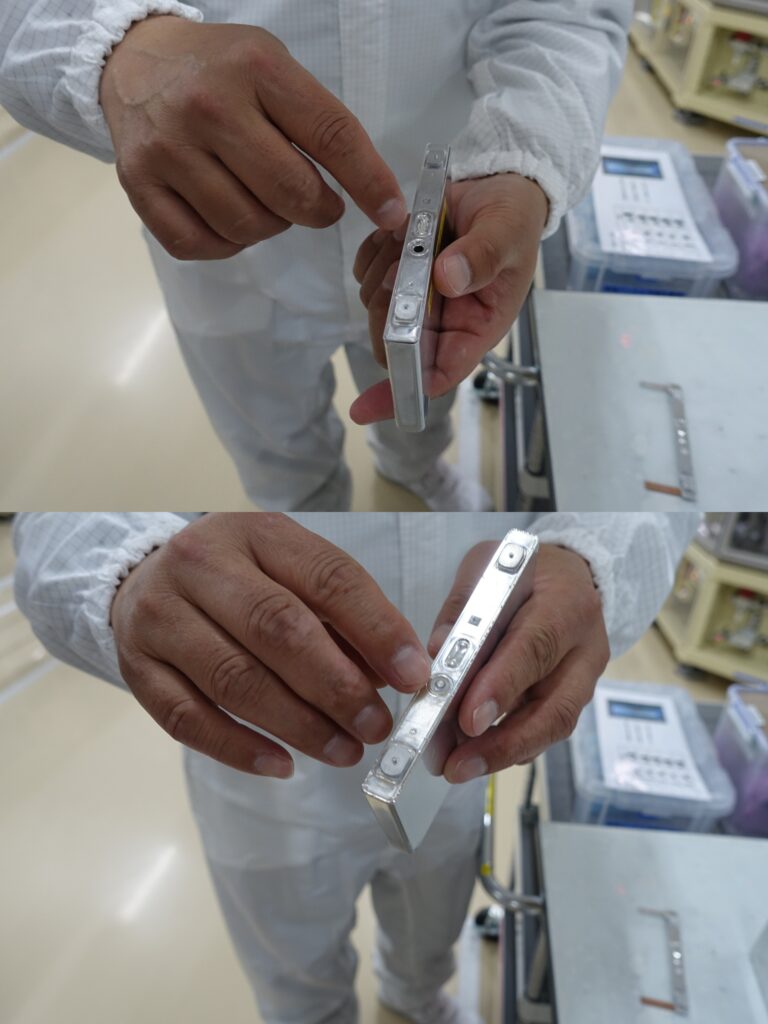
受け継がれる日本のものづくり文化
こうして苦労の末に立ち上げた65Dは、PPESの国内工場や中国工場など色々な拠点の地域で生産され、世界中のお客様に届けられています。その主力工場となるPPESの徳島拠点では、地元から約100名の新規採用を行いました。こうした採用方針には、地元の雇用に貢献したいという考えがありました。
「若い社員が非常に多い。本当に、日々成長しているっていうのが実感できます。私だけでなく、グループ長も係長班長も、若い社員の成長を自分のやりがいに感じています。生産性や競争力は、人が成長することでおのずとついてくるものだと思います」(K. T.)
地域での活動は採用だけではありません。PPESでは事業所のある拠点で出前授業など地域交流活動も積極的に行っています。「近い将来、彼らがカーボンニュートラルや様々な難しい課題に立ち向かう人財になって、どこかで活躍してくれるとうれしい」と、Y. O.は言います。
日本の電池産業が培ってきた「強い現場」は、世代や地域を超えて受け継がれています。
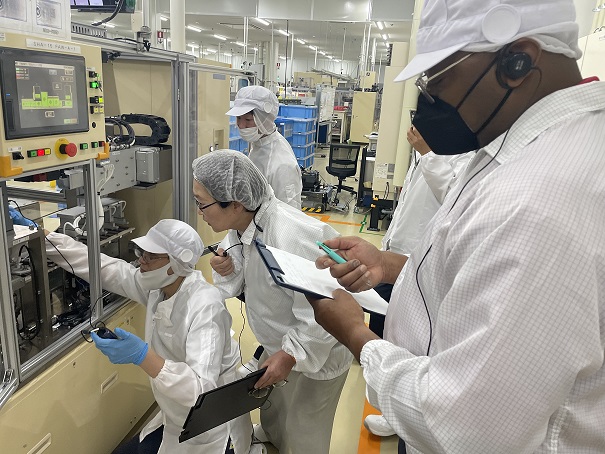
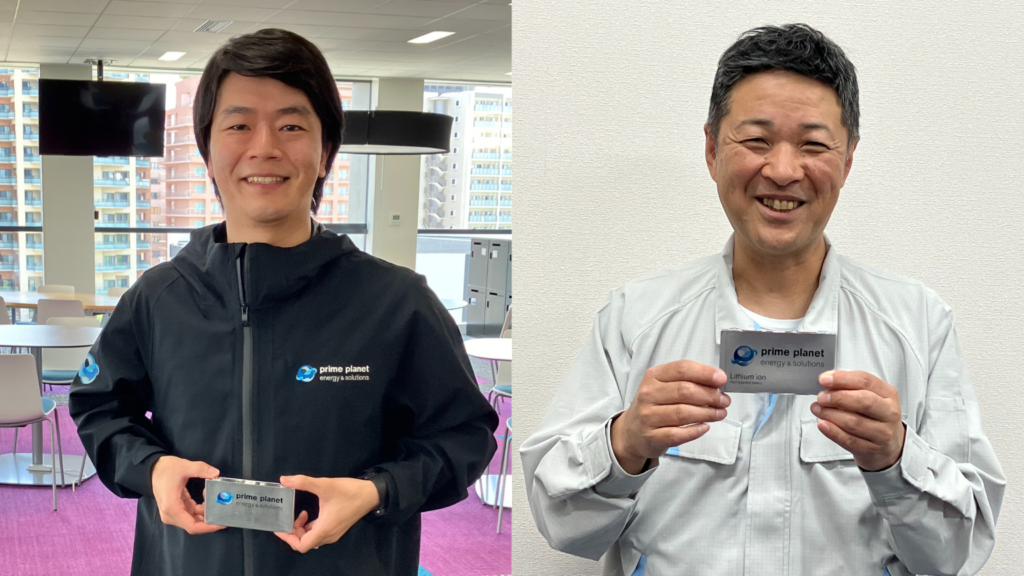